コスト・納期の半減で印刷電子回路が本領発揮
「全ての基板を置き換える」フレキシブル基板で産業を変革するAgIC
大企業の単純な横連携では、イノベーションを創出できない
「これこそがスタートアップだからできた部分。我が社が行っているのは、まったく新しい製造方法。結果的に現在プリント基板の分野で競合はいない。大手が持っている技術の転用では、こちら側へ参入することはできない。というのも、いままでのプリント基板の製造技術と私たちの印刷ベースの技術では、まったくそのプロセスが変わっているため、既存企業が技術をがらっと変えることは難しい」(清水氏)
清水氏によれば、十数年以上前から、アメリカでも日本でも国家主導で、回路を基板に積み上げて作るプリント基板の開発に取り組んだことがあるが、どれもうまくいかなかったそうだ。既存の業界横断で必要なメーカーを集めただけでは開発できない。このようなイノベーションを生むためには、印刷媒体の紙やフィルムメーカー、インクなどのケミカルメーカー、メッキのメーカー、印刷機などのハードメーカーなどなど、クロスボーダー的にいろんな企業を集めて開発しなければならないが、大手企業の連合ではスピード感もなく、なかなか前に進まない。
実はこのような各々の分野をインテグレーションして新たな技術を生み出すことこそ、スタートアップにうってつけなのだ。従来の技術にこだわる大企業では、各社それぞれの思惑を持っているため、すべてを捨ててまで新たな分野を創出できない。またそういう大企業だからこそ、逆にAgICの技術が必要になってくるという。
「新サービスはメーカーからの評判が非常に良い。とくにアンテナ・メーカー。いま携帯端末やICカードに入っているアンテナはほとんどすべてがフィルム型だが、このアンテナの開発には莫大なコストがかかっている。というのもアンテナ作りはシミュレーションが非常に重要で、図面通りに作れば最初から100%がわかるわけではなく、実際に作って、その特性を計測しなければ最終性能がわからない。だから少しずつ形状を変えては製作し、特性を計測する必要がある。
サイクルとしては、いままでは製作に約2週間、コストも10万円単位でかかっていた。それがAgICでは、3日以内に2~3万円で製作できる。じつは設計データがあれば最短1日でできてしまうが、厳しい検品で出荷できないこともあるため、念のため時間をいただいている。今後製造プロセスが安定すれば、翌日にも出荷できる」(清水氏)
大手は得てして研究・開発費が高い。それには人件費だけでなく、大手が基板の試作を外注して、その完成を2週間ほど待っていることがボトルネックになっている。その間、研究は次のステップに進めない。高給な研究者の手が止まってしまうため、コストがかさんでしまう要因となってしまうわけだ。
「もちろんいまでも超高速で製作するメーカーもある。24時間対応の工場で作業しているが、1回あたり30万円ほどのコストがかかってしまう。大手メーカーからは、翌日に来るのであれば10万だろうが20万であろうが払うと言われている。人件費を考えるとそれだけの価値はある」(清水氏)
現在プリント基板の製作は、ほとんどが中国だという。しかし実際の製品に使用されるプリント基板がAgICのものに置き換われば、時間がかかる海外で製作する必要はなくなる。製造コストも輸送コストも、そして時間までもが節約できるのであれば、製造業の競争力をより高めることができる。
まずは試作の分野でメーカーの開発コストを半分に
AgICの技術的アドバンテージは、地道に研究・開発を行ってきたこの3年間で作られたものだ。インクジェット印刷と銅メッキによる独自のフレキシブル基板として結実したが、これから数年間は、さらにフレキシブル基板の性能を上げることに注力するという。
「ビジネスを考えると自動車や家電、デジタル機器で使用されているフレキシブル基板をAgICのものに置き換えることが最も重要なこと。フレキシブル基板だけでマーケットは3兆円とも言われている。ただフレキシブル基板はまだまだコストが高い。これを半分にしていきたい。現状では生産キャパシティーの問題もあるので、まずは試作の分野でメーカーの開発コストを半分にし、このマーケットを独占したい」(清水氏)
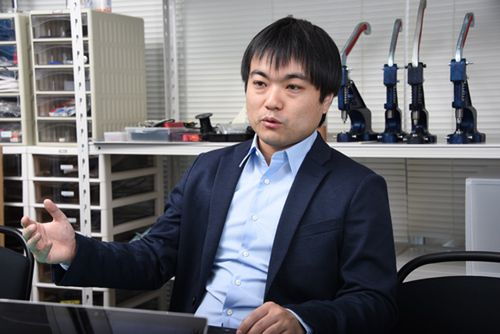
2~3年で試作分野を独占していくという計画は、圧倒的コスト競争力を考えるとあながち無理な話ではない。しかも大手の参入しにくい分野でもある。
「このような製造技術の開発は、大手の場合、確定した顧客がいないとなかなか取りかかれないし、そもそも製造設備を作ることができない。我々の場合は少量を使っていただき、顧客からのフィードバックをもらう。そうして製造技術をチューンナップしていく」(清水氏)
もちろん、「検査技術など量産化に向けて、必要な工程はまだいくつも残っている」と清水代表は言う。たとえば現状でのデメリットでは、最大瞬間耐熱が200℃のため低温ハンダを使わなければいけない点や、年単位での耐久性データなどは時間的な制約で取れていない。しかしそれらクリアしていくべき課題が明らかなため、地道に解決していくのみとなっている。そして、そのひとつひとつがAgICのアドバンテージにもなるというわけだ。
週刊アスキーの最新情報を購読しよう
本記事はアフィリエイトプログラムによる収益を得ている場合があります