コスト・納期の半減で印刷電子回路が本領発揮
「全ての基板を置き換える」フレキシブル基板で産業を変革するAgIC
2017年04月21日 07時00分更新
電子回路を印刷で製造する技術を開発する東大発ベンチャーのAgIC(エージック)。回路が描けるペンとインクが消せるペンなども一般消費者用に販売しており、教育分野での評価も得ている同社だが、現在は法人向けの展開が主となっている。
印刷プロセスで作れる電子回路は、既存のフォトリソグラフィプロセス(感光性物質への露光によるパターン生成技術)よりも製造プロセスが簡略化され、材料も少なくて済むため、製造コストとリードタイムを大幅に下げられるという画期的なものだ。2017年からは、耐久性や耐熱性に優れ、既存のフレキシブル基板とほぼ同等の性能を持つ”印刷と銅めっきを組み合わせた産業用回路印刷サービス”を水面下で開始しており、メーカーからの評価も高いという。
2014年の創業から3年を経たいま、事業の進捗とフレキシブルプリントの未来についてAgIC株式会社の清水信哉代表取締役社長に話を聞いた。
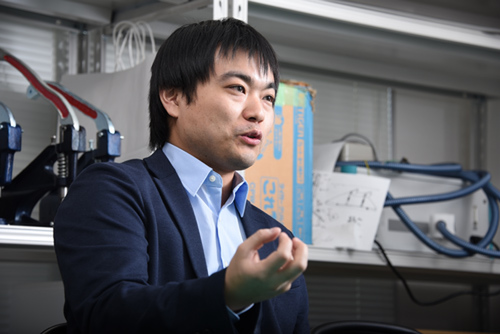
AgIC株式会社代表取締役社長の清水信哉氏
既存プリント基板のリプレースこそが当初からの目的
創業間もない2014年3月、AgICは米国のクラウドソーシングサイトKickstarter(キックスターター)で、電子回路をインクジェットプリンターで印刷できるプロジェクトを発表。3万ドルの目標を大きく超える8万ドルという資金を獲得したことで話題を呼んだ。しかし清水代表としてはそのとき、すでにより高い目標があったと言う。
「もともとのコンセプトは、当社のプリント基板で携帯電話などの中に入っている既存の基板をすべてリプレースするというもの。しかし、耐久性をはじめ技術的に足りない部分が多かった」(清水氏)
外部から問い合わせが入っても、関心を持った会社に評価してもらうと、「このスペックだとちょっと使えない」というフィードバック。創業当初はその繰り返しだったという。結局当時の技術では利用できるフィールドが限られていたため、高度な性能が求められるわけではない顧客として教育分野にも乗り出した。
「電気回路の実験用に指定教材として選ばれ、実際、公立小学校や中学校でも使われるなど、それなりの成功を収めている。しかしそれだけでは成長できないので、並行して技術的に足りない部分を高めるべく技術開発を進めていった」
そのようにして創業から3年。2017年にようやく本格的に法人向けにフレキシブル基板の製造サービスを提供できるところまで来たという。AgICの社員は現在もわずか9名。スタートアップにとって、3年は短いようで長くもある。
競合がないリーディングカンパニー
「この分野では、じつはまだ理論的にわかっていないことも少なくない。インクやメッキなど、こういう添加物を入れたらこういう結果が出るというのは、理論ではわからないことのほうが多い。今後いろいろな方向へ発展していくような技術の開発に関しては、このくらいの人数がちょうどいい」と清水代表は語る。
AgICでは、専用の印刷機を内製し、その後、印刷媒体として紙をはじめさまざまな素材とのマッチングを探っていくという地道な作業を繰り返している。そういったなかで、技術的なマイナス要因を取り除き、さらなる新技術を開発しているという。法人向けサービスでのブレイクスルーは、「銀を印刷したあと、銅メッキによって導電性金属を形成する技術」を確立したことだ。
立ち上がった新技術は、AgICフレキシブルプリント配線板「AP-2」として展開。既存のフレキシブル基板の製造サービスに比べてコスト半額以下・納期も半分という展開を行っている。現在はクローズドでの製造サービスを展開しているが、まもなく一般公開予定だという。
「プリントした銀の回路の上に銅メッキを重ねるという技術の開発がポイント。メッキのメーカーとも共同で実験を繰り返した。我々の銀を使ったインクでは、インクジェットプリンターでプリントでき、またペンで書いても速乾で非常に使いやすくできている。しかし、耐久性と電気抵抗の部分で法人向けとは言い難い。これを銀に銅メッキすることにより抵抗値が下がり、流せる電気の量が格段に大きくなった」(清水氏)
AgICが磨いてきた化学分野の技術は、ひたすらに仮説からの実験を繰り返して、たまたま良い製品ができあがるということの繰り返しだそうだ。試行錯誤を繰り返して最適な製品はできあがるが、その背景理論はよくわからないといった状態もいまだにある。強度を高めるメッキの技術においても試行錯誤の毎日。厚みの許容範囲がどのくらいなのか、その精度を出すのにはどうすればいいか、日々挑戦を続けている。
現在ではメッキする銅の厚さも変えられ、それこそ当初の目標であった携帯電話で使用できるほどの電気量も流せる基板をつくることができるようになっている。また、銀だけでそれだけの厚みの回路をつくると莫大なコストがかかるが、原価が安く導電率も銀と同様に高い銅を使用することにより、大幅なコストダウンが期待できるという。
本来は銅そのものをプリントできればいいのだが、銅ならではのさまざまな要因でそれは難しい。その点、加工しやすい銀をプリントし、それを”シード”にして銅メッキする方法は合理的だ。
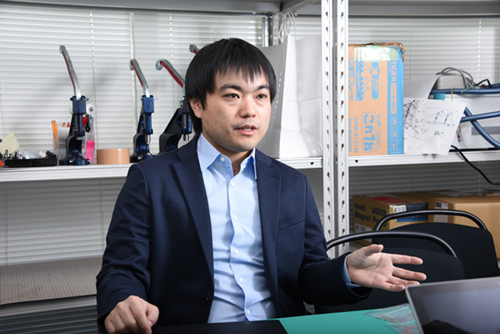
だが、そもそもこのような既存の基板をリプレースするような研究開発は、スタートアップだけが狙ったものではない。世界中の大企業がこれまで挑戦してきたハード開発におけるイノベーションだが、いままでこれらの方法が数々の大企業では生み出せなかったのはなぜなのか。
週刊アスキーの最新情報を購読しよう
本記事はアフィリエイトプログラムによる収益を得ている場合があります